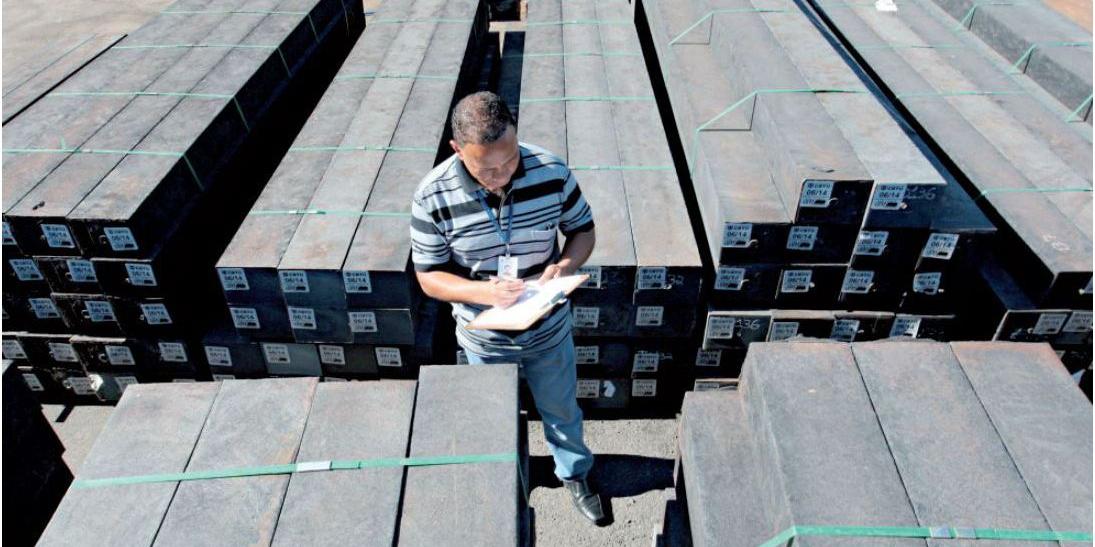
O metrô de Belo Horizonte vai utilizar dormentes que trazem duplo benefício ao meio ambiente e ao cidadão que paga pelo serviço: a cada quilômetro de linha férrea em que é aplicado o material, 750 árvores deixam de ser cortadas e 158 toneladas de resíduos plásticos são recicladas. Os lotes de dormentes poliméricos chegaram aos pátios de manutenção, ao lado das estações Eldorado e São Gabriel, para substituir a madeira nos trilhos.
Segundo o coordenador de edificações e vias da Superintendência de Trens Urbanos de BH, Reinaldo Eustáquio Araújo, a troca gradativa dos mourões de madeira da estrutura torna a base da via férrea mais sustentável e com maior durabilidade.
O lote adquirido corresponde ao consumo de um ano de manutenção da via comercial. “Não comprovamos ainda a vida útil, mas a CBTU aplicou o material em Recife há sete anos e não houve problema”.
Araújo prevê um prazo de 20 anos para substituir todo o trecho em BH. Em 16 km da via férrea Vilarinho-Eldorado há mais de 5 mil dormentes. O consumo é de 269 dormentes/ano.
De acordo com Araújo, o afrouxamento do parafuso na madeira exige reaperto e a manutenção seguinte é virar o dormente de lado. Isso dá ao dormente de eucalipto vida útil de apenas 1,5 a 2 anos. “Já chega fragilizado e muitas vezes apresenta rachaduras quando é retirado do estoque”.
Desde 2012, a operadora estuda a aplicação da nova tecnologia no sistema de trens urbanos da capital, na expectativa de aliar a preservação dos recursos naturais à alta performance técnica e ao baixo custo de manutenção.
Confirmada a superioridade do material, a madeira deixará de ser elemento estrutural da via permanente. O fabricante argumenta que o custo do dormente polimérico é comparável ao de madeira de lei, mas em relação ao dormente de eucalipto, custa a metade e dura 20, 30 anos.
O diretor da Wisewood Soluções Ecológicas, Bruno Higel, afirmou que o dormente plástico e seu viés sustentável ainda é pouco considerado pelas ferrovias no país. “Isso ajuda a mudar o mundo”, observou.
Mesmo assim, a tecnologia industrial que oferece dormentes 100% brasileiros chegou aos portos de São Luís (MA) e Tubarão, em Vitória. Além de evitar o corte de madeira de lei, a nova tecnologia impede que um volume significativo de resíduos seja destinado aos aterros e lixões espalhados pelo país.
Reciclagem
Os dormentes poliméricos são feitos a partir da reciclagem de pneus velhos, garrafas pet e outros materiais. Cooperativas, sucateiros e indústrias fornecem a matéria-prima. Os rejeitos são lavados, moídos e derretidos. Na formulação com as propriedades necessárias ao dormente, essa “massa” é colocada em formas e “curada” por dois dias para solidificar o produto.
Novo produto supera o aço, a madeira e o concreto
A ‘madeira plástica’ não contém nenhuma substância tóxica dentre as encontradas na madeira tratada, segundo a empresa Wisewood. É um produto moderno, sustentável e ecologicamente correto ao evitar o desmatamento e poder ser novamente reciclado.
“Entre as alternativas disponíveis para fabricar dormentes, a madeira gera um problema sério de destinação final. Já o aço e o concreto trazem malefícios ao meio ambiente em termos de energia”, disse o diretor Bruno Higel.
Segundo ele, para instalar os dormentes de plástico são utilizadas as mesmas ferramentas dos dormentes de madeira. Já os de aço e concreto exigem outro lastro e outras ferramentas.
Economia
O diretor assinalou que o processo de fabricação emprega mão de obra direta e indireta, gerando renda para todos os níveis sociais, pois a matéria-prima é o lixo reciclável, mecanismo de ganho para uma legião de pessoas que tiram seu sustento desta atividade.
Nas contas de Higel, um dormente de plástico pesa 110 quilos. “A cada quilômetro são utilizados 1.800 dormentes, o que significa economizar 158 toneladas de resíduos plásticos. Com 170 mil dormentes instalados são retiradas 15 mil toneladas de plástico do meio ambiente”, disse.
A Wisewood é pioneira na produção de ‘madeira plástica’ em escala industrial e referência na fabricação de resina termoplástica reciclada no país. A fábrica fica em Itatiba (SP) e desde 2007 instalou os primeiros dormentes em vias férreas de São Paulo, Minas e Rio de Janeiro.
Ela produz 8 mil peças por mês e tem capacidade instalada para fabricar 40 mil/mês de plástico reciclado com maquinário de última geração. “Nossos produtos foram desenvolvidos para substituir o uso da madeira convencional e todos são provenientes do lixo plástico pós-uso, por isso o nome ‘madeira plástica’”, observou.